Some Of Indonesia Furniture Manufacturers
Some Of Indonesia Furniture Manufacturers
Blog Article
Not known Incorrect Statements About Indonesia Furniture Manufacturers
Table of ContentsThe Facts About Indonesia Furniture Manufacturers UncoveredThe Buzz on Indonesia Furniture ManufacturersNot known Details About Indonesia Furniture Manufacturers Getting My Indonesia Furniture Manufacturers To Work10 Easy Facts About Indonesia Furniture Manufacturers Explained
However, there are some downsides to purchasing from a furnishings producer. For one, you may have to wait longer to obtain your furnishings since it's being made to order. Furthermore, you might not have the ability to see or touch the product before you purchase it. A furnishings store is a firm that markets furniture made by numerous manufacturers.When you purchase from a furniture retailer, you're buying an item of furnishings that's already been made and prepares to be delivered to your home. Among the benefits of acquiring from a furniture store is that you can often see and touch the product before you purchase it.
At BH Furniture, we think in establishing new standards for excellence in the production of commercial furniture - Indonesia furniture manufacturers. Our commitment to technology has actually led us to accept advanced automation modern technology, transforming the method we make furnishings and moving us to the center of the sector. Gone are the days of hand-operated labor controling the manufacturing floor
Our equipment functions perfectly, assisted by the accurate parameters set by our skilled designers, ensuring constantly top notch result. State goodbye to production delays and overtime costs. Our automated systems run tirelessly, 24/7, assuring a stable and undisturbed operations. This implies we not only satisfy however exceed shipment due dates, providing our clients with a degree of reliability that conventional manufacturing techniques just can not match.
Little Known Questions About Indonesia Furniture Manufacturers.
Our manufacturing capacity has risen, enabling us to meet the needs of also the biggest projects without compromising on high quality. As your companion in industrial furnishings solutions, we can easily scale our result to accommodate your needs, despite the scale. While traditional manufacturing depends greatly on manual work, our automated systems have considerably decreased our dependence on a huge labor force.
Furnishings production is a complicated process that entails different stages, from making and product selection to manufacturing and assembly. At each stage, there is an opportunity of issues or mistakes that can endanger the quality of the final item. To ensure that furniture is of high quality, furniture manufacturers apply quality assurance procedures to identify and fix any type of concerns that may arise during manufacturing.
The inspection process must cover different elements, such as assembly, surface, colour, layout, packaging, labelling, and marking. By implementing a strenuous examination procedure, suppliers can guarantee their products meet the essential high quality, safety and security, and durability requirements. They likewise supply the adaptability to attend to problems and make corrections prior to finishing the final item.
Furniture top quality requirements are sets of standards and demands for furniture manufacturing. They specify the called for top quality level of furniture manufacturing and cover facets such as safety, resilience, stamina, and environmental impact.
An Unbiased View of Indonesia Furniture Manufacturers

To guarantee their furniture products can withstand numerous weather condition components, consisting of sunlight, rain, snow, and wind, suppliers need to think about internationally acknowledged requirements that consist of evaluations and screening. Here are some of the requirements to bear in mind: ASTM F1561-03 is a worldwide standard created by the American Section of the International Organization for Testing Materials (ASTM).
UL 962 is a worldwide safety requirement established by Underwriters Laboratories (UL), an independent worldwide supply security options business. The standard applies to house and business furnishings, including outside furniture.

All about Indonesia Furniture Manufacturers
It aids to identify issues in the furnishings and review its efficiency and compliance with the needed quality standards. Below are the actions right here for conducting laboratory screening for furniture: Producers gather samples of furnishings components that need testing. These samples normally represent the various kinds of furnishings that they create.
This might include a combination of various examinations, including strength screening, resilience testing, safety and security screening, and ecological influence testing. The examples are after that evaluated for numerous quality parameters, such as toughness, resilience, safety and security, and ecological impact. The outcomes are after that assessed to identify whether the More Bonuses products fulfill the called for high quality standards.

Generally, every retail shop furniture is different. Layouts conference client benefit Making the most of space use in storage space, display screen, step, guest seats and sidewalks Making certain convenience of accessibility to items for trials and purchase Designing modular furnishings that is easy to relocate and renovate Fulfilling safety requirements of customers A quick TAT from design to production and installation with minimal mistakes can help resolve the above concerns.
Indonesia Furniture Manufacturers - Questions
A designer can understand the market fads and be ready with cutting-edge layouts in advance of time. Review here: Just How DriveWorks Helps You to Reduce Lead Time in Production Developers commonly have to change the shapes and sizes of furniture at a minute's notification. These might have various visual and useful requirements like front workdesk, and maintenance workdesk that vary in dimensions.
on a common platform. This assimilation of sales and ERP functions brings even more exposure on cost and rates. It basically passes on CPQ like functionality and enables creating quick quotes and amounts for budget assessments and finalizing orders. Indonesia furniture manufacturers. DriveWorks can auto-generate manufacturing store illustrations with BOMs and DXFs for sheet cutting and punching
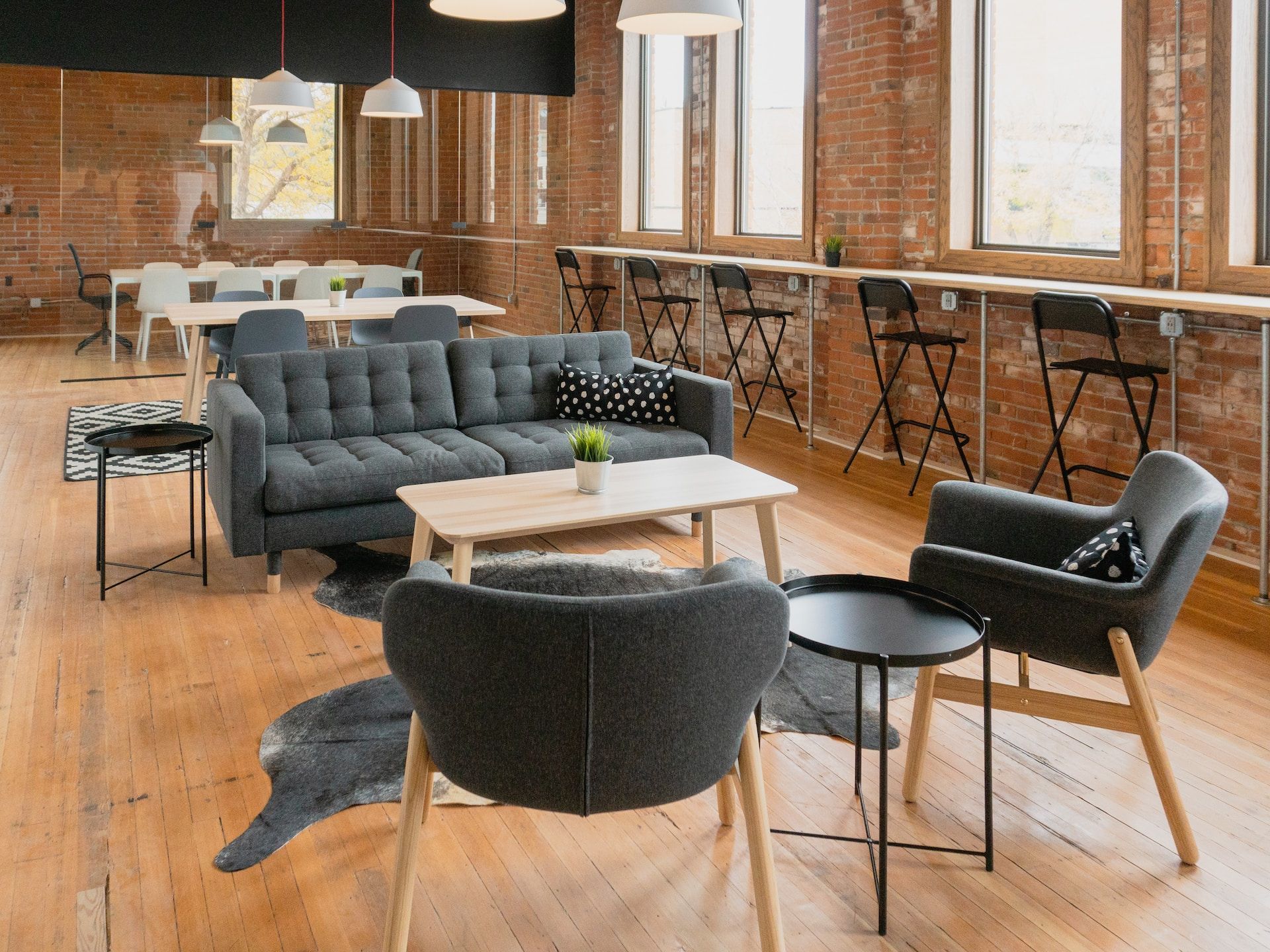
It is an extremely competitive market, with companies striving to keep up with transforming customer needs and the most current technological patterns. Today's customers are more likely to prefer furniture that is customized and made with lasting materials.
Report this page